HDPE Fabrocated 90°Bends Pipe Fittings
***Advantages and welding of PE butt fusion welding 90 degree elbow pipe fittings:
PE butt fusion welding 90 degree elbow pipe fittings is light, which is more common for partial
application pe80 pe100 grade level and two standards , including :
PE80 density of about 0.94 g / cm 3, PE100 density of about 0.96 g / cm 3 ;
Easy thermoplastic - easy to process ( such as injection molding, extrusion molding
Remanufacturing easy recycling
Good resistance to radiation and chemical stability
Good resistance to cold , the temperature can be -40 ℃ to +40ºC
Excellent electrical insulation properties , is not affected by electrolytic corrosion
Malleable - extended break PE80> 700% PE100> 600%
Anti- erosion resistance - 8 times better than steel
Approximately half of the low thermal conductivity of glass
Smooth surface , unlike the role of metal pipes rust easily with oxygen crusts
pe pipe connection into fused pipe connections and fittings connected to melt , the more ordinary side,
the other , as well as socket connections, this method is applied to a small size.
1 , fused connection : Follow these steps: First check , and then is cut pipe , pipe fittings joints clean , scrape the oxide layer , connecting the two parts of the tube and pipe fittings , calibration welder , welding parameter adjustment in accordance with the welding voltage, welding Dimensions , electricity, welding, and then finally cooled.
2, the hot melt connection : the inner surface of the pipe surface and the pipe is inserted while the welding is non-rotating die head is heated for a few seconds , then quickly removed and welding device , the heat pipe has a fast vertical insertion tube , packing, cooling to .
3 , socket connections, relatively simple, not elaborate here .
***Specifications of hdpe butt weld 90 degree elbow with five segments pipe fittings:
 |
Size | D(mm) | H(mm) | L(mm) |
L500 | 500 | 1055 | 350 |
L560 | 560 | 1145 | 380 |
L630 | 630 | 1326 | 440 |
L710 | 710 | 1447 | 480 |
L800 | 800 | 1507 | 500 |
L900 | 900 | 1658 | 550 |
L1000 | 1000 | 1808 | 600 |
L1200 | 1200 | 1959 | 650 |
***Basic performance of raw materials for pipe fittings
Paramenter | Units | Requirement | Test Value |
Density | kg/m³ | ≥930 | 23ºC |
Melt flow rate | g/10min | 0.2~1.4 | 190ºC,5kg |
Thermal slaility (OIT) | min | >20 | 200ºC |
Volati lematter content | mg/kg | ≤350 |
|
Moisture content | mg/kg | ≤300 | ASTM D 4019:1994a |
Carbon black content | % | 2.0~2.5 |
|
Crbon black dispersion | grade | ≤3 |
|
Gas proof components | h | ≥20 | 80ºC,2MPa(Hoop stress) |
Resistance to slow crack growth (En>5mm) | h | 165 | 80ºC,0.80MPa(Testing pressure) 80ºC,0.92MPa(Testing pressure) |
***Performance requirement of pipe fittings
NO. | Item | Requirement | Test value |
1 | 20ºC hydrostatic strength | No damage, no leakage | Hoop stress: PE80 10.0MPa PE100 12.4MPa Testing temperature: 20ºC Testing time: ≥100h |
2 | 80ºC hydrostatic strength | No damage, no leakage | Hoop stress: PE80 4.50MPa PE100 5.40MPa Testing temperature: 80ºC Testing time: ≥165h |
3 | 80ºC hydrostatic strength | No damage, no leakage | Hoop stress: PE80 4.50MPa PE100 5.40MPa Testing temperature: 80ºC Testing time: ≥1000h |
4 | Tensile strength of butt-fusion pipe fittings | Test to destruction: Flexible is good | Testing temperature:23ºC±2ºC |
5 | Welding strength of electro-fusion pipe fittings | Percentage of brittle peel: ≤33.3% | Testing temperature:23ºC±2ºC |
6 | Oxidation induction time | >20min | 200ºC |
7 | Melt flow rate | Tube melt rate of change not exceeding ±20% of the raw material | 190ºC, 5kg
|
***hdpe butt welding machine
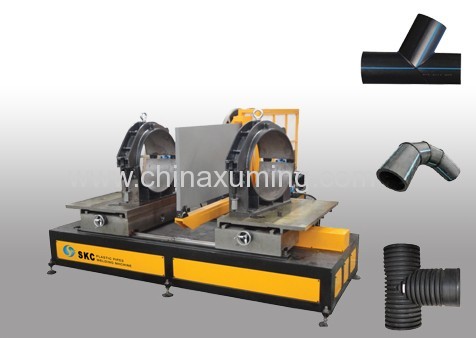
***Exporting countries
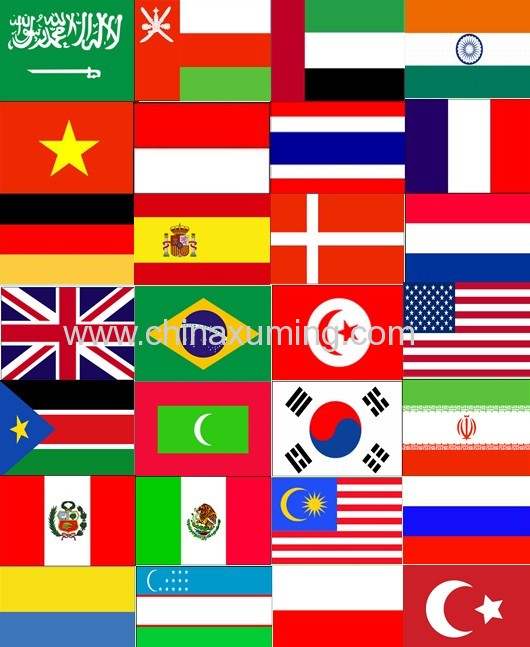